- Home
- Company
- Media Relations
- Blog
- Cast-in Channels-A Shift to Pre-Installed Anchors
Cast-in Channels - A Shift to Pre-Installed Anchors
Know about the construction industry’s seamless transition to cast-in channels and how they provide unparalleled flexibility in the business.
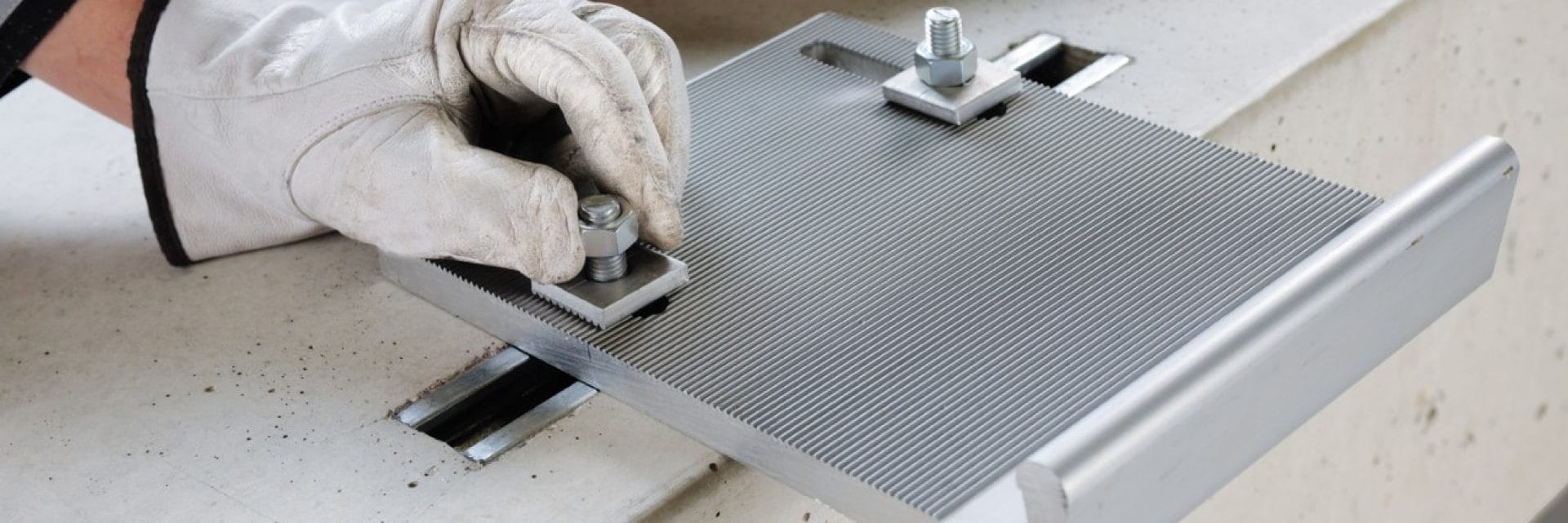
The Emphasis on Detailed Design
Compared to ten years ago, today’s construction industry moves astonishingly fast. Worldwide, project timelines are reducing and buildings are erected in record time, all without compromising on design and stability. Buildings itself have greater complexity in their architectural layout, often integrate reinforced concrete and structural steel elements, are clad with intricate curtain wall systems as building envelopes, contain a plethora of building (MEP) services, and require designations as green, sustainable, or even zero-carbon in some cases for their entire lifecycle. Thus, a project today requires careful and detailed planning in its conceptual stages to enable clockwork-like construction, and create sustainable value for all stakeholders involved.
Fastening Systems
All buildings contain a substantial number of fastening systems to securely integrate primary-primary & primary-secondary connections such as connecting structural steel to a concrete member, a curtain wall segment to the slab’s edge, or building services to the main structural members. Fastening systems differ according to their load capacities and the three distinct types of installation techniques: (a) cast-in-place, (b) post-installed, and (c) direct fastening.
- Cast-in-place: components positioned securely in the reinforcement before casting;
- Post-installed: anchors are installed in holes drilled into concrete already cast;
- Direct installation: nails or studs driven into the concrete or steel base material with powder cartridges or pneumatic action.
Pre-plan with cast-in systems
Cast-in systems use a wide range of inserts, with or without baseplates: for instance, lifting inserts for transporting precast concrete components, anchor channels, embedded plates with headed studs, bent rebars connected to internally threaded rods, and customised components for hanging heavy façade panels and securing masonry.
Following the ethos of detailed planning during the conceptual stage, cast-in-place fastening systems allow the greatest advantage in situations where the external load’s location is known and, thus, accommodated in designing the reinforced concrete member through suitably positioned reinforcement. Compared with the other two systems, cast-in-place does not require any activity after casting the concrete, which neither damages the concrete base and embedded reinforcement nor reduces site productivity – this is essential in both post-tensioned and high-strength concrete members. However, it does require extra layout and planning required during the conceptualisation of these systems and there is a potential of erroneous placement during execution, which can be mitigated with proper training at site.
Hilti Cast-in Anchor Channels – Unparalleled Flexibility
Anchor channels consist of a cold-formed, a hot-rolled, or (with Hilti Anchor Channels) a temperature-controlled and -rolled channel equipped with an integrated round-headed rigid anchor tied to the reinforcement prior to casting the concrete. The channel is filled with a low-density polyethylene (LDPE) foam to prevent concrete intrusion, which is ripped out after curing. In the channel itself, special T-headed bolts allow the installation of various components.
These channels allow flexibility on an unparalleled scale not just with positioning of the fixture itself and the attached T-bolts, but also enables positioning of the anchor channel very close to the edge of concrete members. Compared to a post-installed system, this system can carry comparatively higher loads, since the closer post-installed anchors are to the edge, the lower the load they carry. Flexibility here also implies eliminating drilling and reducing the installation time of façades and lifts, enabling architects and façade consultants to pre-plan layout and elevations, adjust the fixing position, and anticipate the connection’s load. Consequently, this: improves overall project efficiency; allows carrying of higher loads; and uses an ETA-approved and well-designed system solution, suitable for use even in post-tensioned slabs.
Across all industries and projects, Hilti’s Cast-in Anchor Channels (HAC) see use in a variety of fastening applications, such as (but not limited to):
- Building (MEP) services in pre-stressed or post-tensioned concrete buildings and bridges
- Façade brackets for unitised curtain wall glazing
- Balcony and hand rails
- Joining together precast concrete components such as internal wall partitions
- Guide rails and brackets for lifts
- Installing machinery and supporting MEP services in industrial and power generation projects
- Overhead lines, signal lights and ventilation systems in tunnels and metro projects
Selection and Design Criteria
While selecting the appropriate Anchor Channel depends upon three factors – correct sizing of the channel, its T-bolt, and assessing the required corrosion protection during temporary and permanent exposure conditions – the correct sizing depends on the following factors:
● Magnitude of the applied load
● Direction of this load
● Nature of the load (static/dynamic/seismic/etc.)
● Proximity to the edge, thickness, and grade of the concrete member
● Details of steel reinforcement
● Bracket/fixture thickness to be attached to the anchor channel
● Presence of grout underneath the bracket due to construction tolerances
The factors above also influence the design, which is undertaken according to the limit state approach of reducing the characteristic resistance of the channel, concrete, and the reinforcement, while increasing the working tension and shear loads.
Conclusion
Hilti offers architects and engineers full guidance on selecting and designing the right anchor channel system according to the right connections under the right loading conditions so no matter the location or the loading, you can be assured that your structure will have the highest level of safety. Look out for our next article on this topic, where we will cover the design parameters influencing the behaviour and performance of Anchor Channels.
Also Read: How to Install Cast-In Anchor Channels
ASK AN ENGINEER