Combining state of the mind with the state of the art
Rebooting construction productivity for the new normal
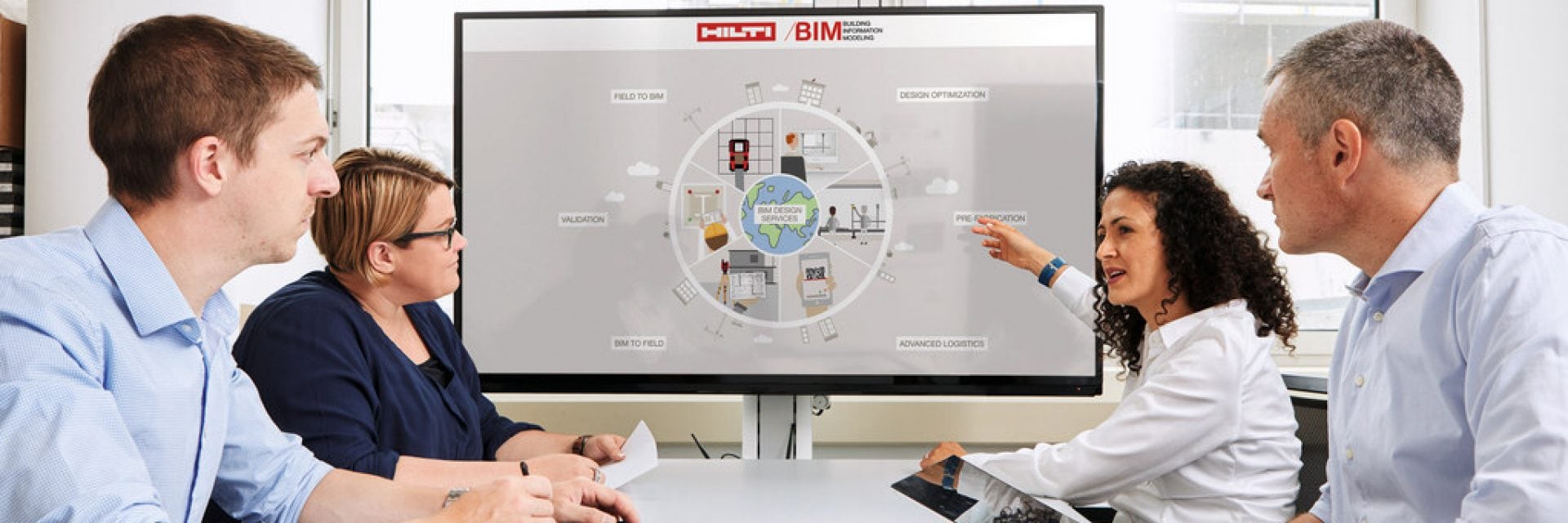
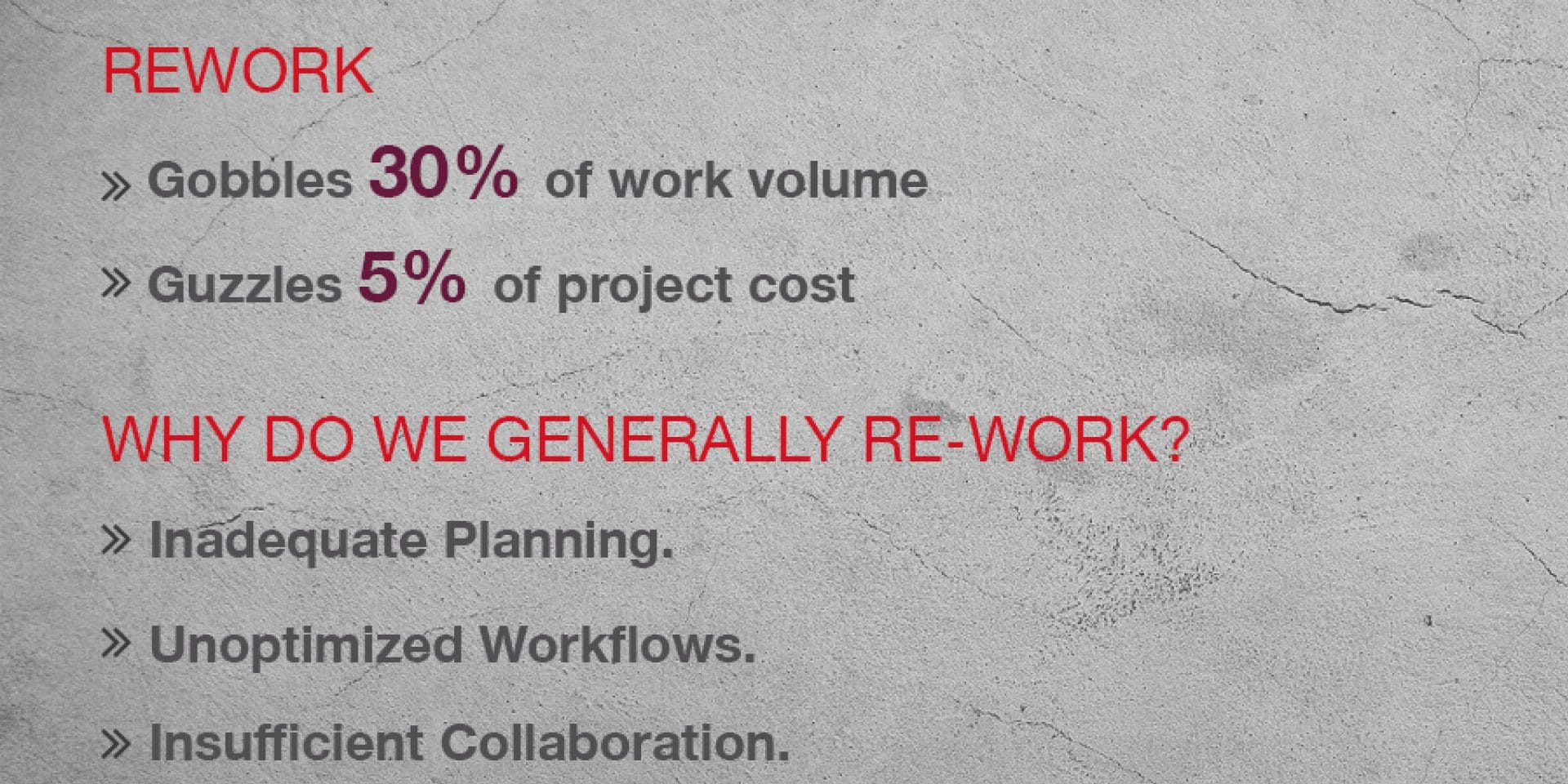
CURB THE COST
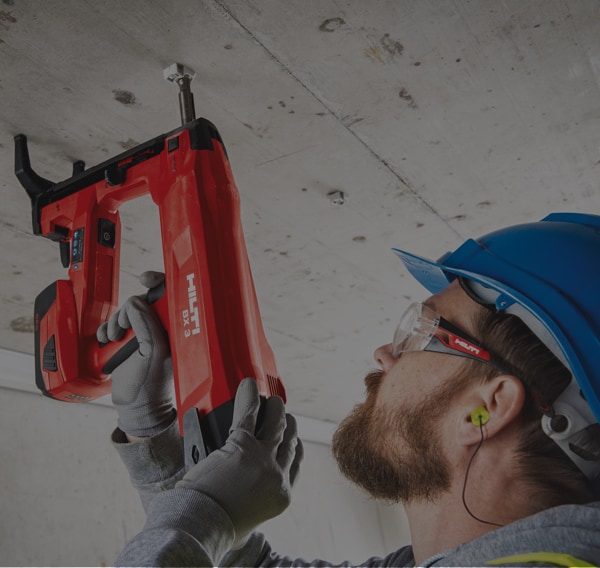
Mastering TCO
Improving productivity by 60% can save upto 38% of cost by trimming time, labour and material. In the NEW NORMAL, organizations must therefore plan tool and technology adoption early, and with a long-term cost optimization approach. This is where TCO comes in. An acronym for Total Cost of Ownership, TCO lets us combat the phantom of Hidden Cost which, according to research, can reach as high as 80% of the overall cost of a project.
TCO is essentially the science (and art - yes, intuition can come handy here) of interpreting expense in the light of the overall project curve, and not just the initial acquisition cost. Purchase can support and accelerate this transformation by evolving into a techno-commercial function (and must be appraised in a new light by construction companies). The habit of favouring the lowest quote, for instance, may not always do the business a favour.
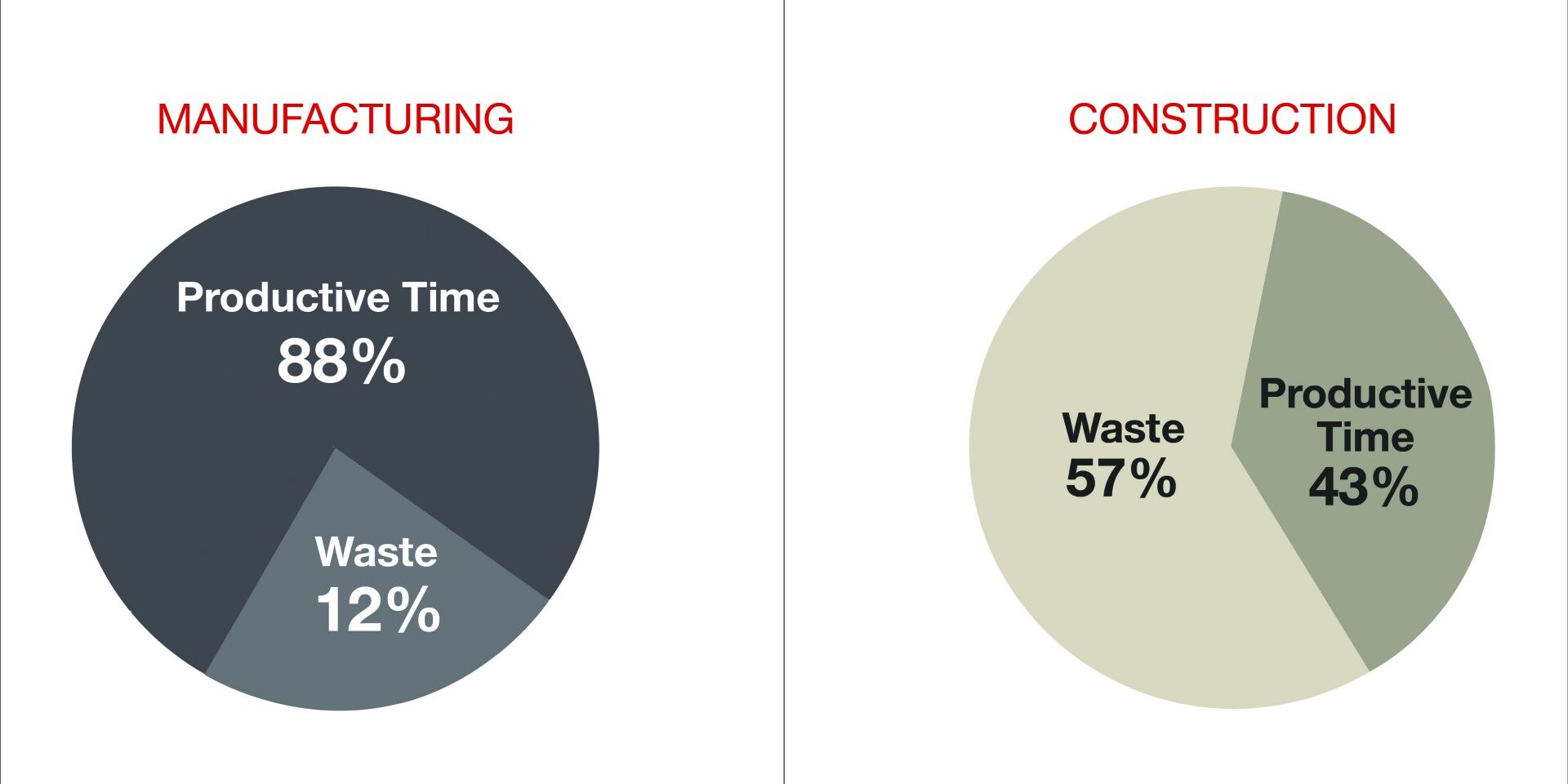